Einleitung
Zu Beginn des Projektes haben wir gemeinsam überlegt, welche funktionalen Anforderungen unsere smarte Mülltonne aufweisen muss. Dazu haben wir nach Modellen von reellen Mülltonnen auf verschiedenen Webseiten für 3D Modellierung gesucht. Malte ist auf ein sehr detailliertes Modell einer Mülltonne auf Thingiverse gestoßen, welches wir als Grundlage für die smarte Mülltonne verwenden wollten. Des Weiteren haben wir anfänglich überlegt eine OLAP-Cube förmige Anordnung von 20 HCSR04 Ultraschallsensoren zu verwenden, wozu wir aber diverse andere Herausforderungen, wie den Bau eines Multiplexers und aufwändigeren Code und das Verwenden von mehreren Level-Convertern hätten berücksichtigen müssen. Im Deckel der Mülltonne sollte der Sensor angebracht werden und das Controllerboard hinten auf die Mülltonne in einer separaten 3D-gedruckten Halterung angeklebt werden. Der Sensor sollte sich ebenfalls in einer 3D gedruckten Halterung befinden und diesen somit am Deckel befestigen.
Das erste Modell
Wir haben somit also das STL Modell der Mülltonne in OpenSCAD importiert und das Modell darin skaliert, damit es den maximal druckbaren Bereich des 3D Druckers im Makerspace von 205mm ausnutzen könnte. Später sollte sich aber herausstellen, dass ein 3D Druck in dieser Form über 25 Stunden dauern würde, was nicht akzeptabel war, da unter Umständen noch Veränderungen am Modell hätten vorgenommen werden müssen. Krischan konnte dies mithilfe der beiden Slicer Ultimaker Cura und UP Studio herausfinden, da diese unterschiedliche Methoden des Slicens anwenden und dies führte auch zum zweiten Problem: OpenSCAD kann keine STL Dateien mithilfe der Bearbeitungsbefehle bearbeiten. Das importierte Modell haben wir stets so behandelt, als sei dies ein importiertes Modul eines OpenSCAD Blocks. Wir haben dazu verschiedenste Dinge ausprobiert: Im Cheat Sheet von OpenSCAD die Dokumentation von der Import-Funktion gelesen, aber nichts zu diesem Problem finden können. Des Weiteren hat Krischan im OpenSCAD Forum nachgeschlagen und dort stand, dass seine bereits anfangs aufgestellte Vermutung, dass die Bearbeitung von STL Dateien in OpenSCAD nicht ohne Probleme einhergehe, geschweige denn überhaupt möglich sei.
Der Prototyp
Wir haben ausgehend von dem Modell von Thingiverse eine skalierte Version erstellt, die wir ursprünglich zu Testzwecken mit dem 3D Drucker testen wollte. Dadurch hätte man feststellen können, ob das Scharnier des Deckels bei diesem Modell auch sauber und funktional ausgedruckt wird, ohne dass wertvolles Filament und Druckzeit verschwendet werden, sollte bereits das kleinere Modell bei dem Test fehleranfällig sein und das Scharnier zum Beispiel aufgrund des Gewichts von Deckel und Ultraschallsensor abbrechen. Daraufhin haben wir uns entschieden das skalierte Modell ausgehend vom Ursprungsmodell als Pappmodell als ersten Prototypen nachzubauen, indem das skalierte Modell digital vermessen wurde. Dies war dann das Ursprungsmodell in 1,3-facher Skalierung des Ursprungsmodells von Thingiverse. Dies konnte dann von Krischan auf Graupappe übertragen werden, welches anschließend mit festem Holzleim verklebt wurde. Für das Scharnier diente ein Strohhalm aus Plastik, welcher mit einem Wattepad umschlossen wurde. Anschließend wurde der Holzleim als Bindemittel in das Wattepad gestrichen, welches wiederum ausgehärtet ist. Dieses Prinzip ist allgemein übertragbar, da ein flexibles und leichtes Material wie Kohlefaser oder Glasfaser in Form von Gewebematten auch mit verschiedenen Epoxidharzen oder anderen Kunststoffen zu einem leichten Kompound-Feststoff in anderen technischen Bereichen wie dem Bootsbau verbunden werden. Abschließend konnten die Watteköpfe von den Q-Tips mit einem Seitenschneider abgetrennt werden, sodass diese für das Scharnier verwendet werden konnten. In den Deckel des Pappmodels konnten nun zwei Löcher gebohrt werden und mit einem scharfen Kartonmesser der Mittelsteg entfernt, damit die beiden Köpfe des Sensors hindurch passten.
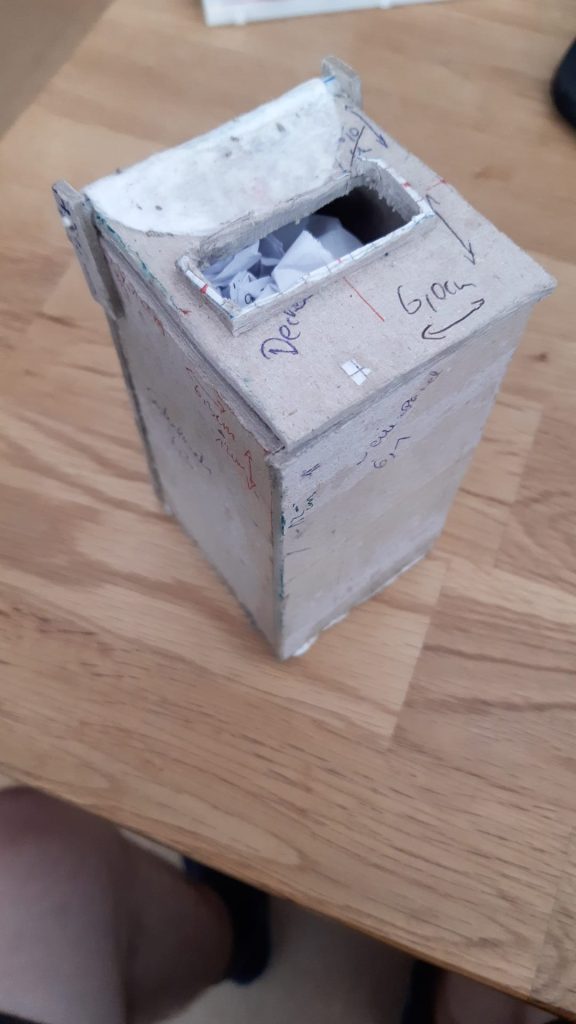
Weitere Probleme
Dieser Prototyp konnte auf Fehler bei dem bereits verkabelten Breadboard geprüft werden.
Deshalb haben wir dann das ursprünglich veranschlagte Design in Gänze überworfen und ein neues Prinzip verwendet. Ein weiteres Problem des Ursprünglichen 3D Druck Modells wäre gewesen, dass wir keinen vernünftigen Platz für den Endschalter im Deckel gehabt hätten und dieser herausgestanden hätte und man eine Hülle für diesen Schalter in den Deckel hätte modellieren müssen. Zudem hätten die Kabel aus dem Modell nach hinten zum Mikrocontroller herausgehangen. Dies hätte aber wiederum das Gewicht des Deckels sehr stark erhöht und das Scharnier belastet.
Umstellung auf Lasercut
Deshalb hat sich die Projektgruppe dann vollständig gegen das Verwenden eines 3D-Drucks für den Hauptteil des Modells entschieden. Florian hat das Lasercutter Modell in Fusion360 erstellt und wir sind mit einem gänzlich neuen funktionalen Design aufgekommen. Krischan hat vorgeschlagen, dass man den Deckel für das Modell nicht mit Hilfe eines Scharnier klappbar machen müsse, da dies zu aufwändig werden könnte. Der Deckel ist in diesem Modell eher ein Kasten mit Aussparungen für einen Kontaktschalter und den Ultraschallsensor. Die ganze Belastung von dem Deckel mit Mikrocontroller und Ultraschallsensor müsste demzufolge von dem Scharnier getragen werden. Die Sperrholzplatten schienen hierfür aber zu dünn zu sein, weshalb wir nicht riskieren wollten, dass die Schrauben die Platten beschädigen. Außerdem hätte man das Scharnier zwar kleben können aber der neue Mechanismus ohne Scharnier ist deutlich weniger fehleranfällig, da hier das KISS-Prinzip (Keep it simple, stupid) angewendet werden kann und das Scharnier ganz entfällt. Ebenfalls konnten wir dadurch die Größe des Modells anpassen und den Hauptteil der Mülltonne von den geplanten 12cm auf 20cm erhöhen.
Erstellung der Modelle
Die ersten Lasercut-Modelle die wir erstellt haben, wurden mit folgendem Online-Tool erstellt, mit dem man problemlos Boxen beliebiger Größe erstellen kann: https://www.makercase.com/#/basicbox
Zum Glück hat zu diesem Zeitpunkt Anatolij mehrere Videos zu dem Thema Lasercutting in Fusion 360 hochgeladen. Da eine Person aus unserer Gruppe schonmal mit Fusion 360 gearbeitet hatte, übernahm er die Modellierung der Mülltonne.
Modellierung in Fusion
In Fusion haben wir erstmal mit der Vorlage von Anatolij angefangen, da diese genau das war, was wir gesucht hatten. Die untere Box ist eins zu eins die Vorlage, bei der wir nur die Maße verändern mussten. Ebenfalls wurde der Deckel entfernt, da dieser an dem großen Deckel angebracht wird.
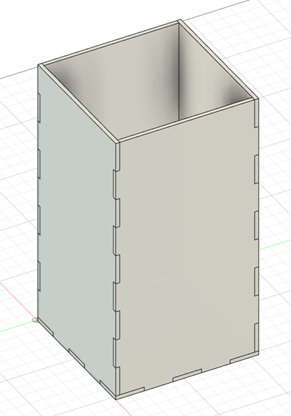
Die obere Box besteht aus der gleichen Vorlage. Jedoch wurde der Deckel der oberen Box und die Seiten so bearbeitet, dass man den Deckel genauso wie den Boden auf die Box draufstecken kann und er somit relativ fest ist und nicht nur aufliegt, wie bei dem eigentlichen Modell. Die obere Box wurde extra etwas unrealistisch groß gemacht, damit die Elektronik genug Platz hat, da wir befürchtet hatten, dass wir die Elektronik nicht auf eine Platine gelötet bekommen. Außerdem wollten wir noch ein Loch oben in den Deckel machen, da wir für das Modell eine Stromversorgung brauchen. Da wir jedoch noch nicht wussten, wie wir die Elektronik im Deckel anordnen, haben wir das Loch erstmal weggelassen und wollten es im Nachhinein noch bohren.
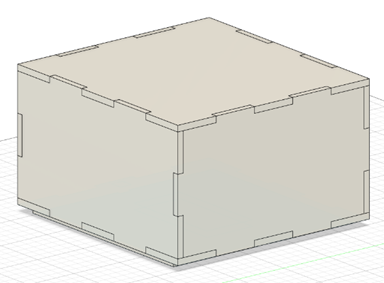
Die untere Seite der Box hat insgesamt drei Löcher. Die beiden kleinen Löcher sind für die Taster mit denen geprüft wird, ob die Mülltonne geöffnet oder geschlossen ist. Diese liegen genau auf dem Rand der unteren Box, wenn man den großen Deckel auf die Mülltonne setzt. Das große Loch in der Mitte ist für den Ultraschallsensor. Das Loch ist extra etwas größer als der Ultraschallsensor, damit er in der Nähe des Deckels angebracht werden kann und er trotzdem nicht den Rand erkennt. Dadurch kann das Problem behoben werden, dass der Ultraschallsensor keine Gegenstände erkennt, die näher als 3cm sind.
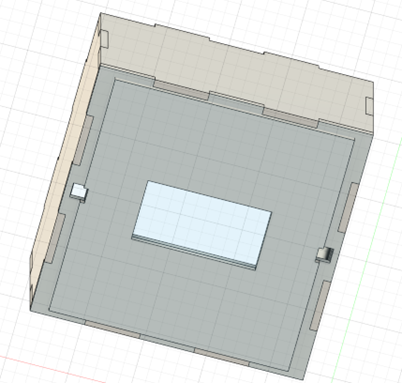
Auf dem Boden ist dann nochmal eine Platte, die die gleichen Löcher hat, wie die andere Platte. Jedoch sind die Maße auf die untere Box angepasst, sodass die Platte genau in die untere Box passt und als Deckel dient. Die obere Box ist von der Breite etwas größer als die untere Box, da sonst nicht die Taster auf dem Rand der unteren Box liegen würden.
No Responses